Integrating digital solutions into mechanical valve safety systems.
Digital captive key solutions for pipeline pigging
By upgrading from a mechanical captive key solution for pipeline pigging to a digital captive key solution, you can achieve higher levels of safety, efficiency, visibility, flexibility, and operator friendliness.
Ensuring pressure protection during pipeline pigging
Common causes of accidents during pigging include over-pressure or exposure to toxic gases caused by incorrect sequence of operation of valves, accidental valve operation, and accidental opening of closure door among other causes. A captive key solution is the industry standard today for pressure protection during pipeline pigging since it functions as an independent layer of safety. The common solution in its current form is composed of mechanical valve interlocks and keys, and a mechanical process control unit (MPCU) to accommodate non-linear sequences. An electronic process control unit (EPCU) is used to incorporate a permissive from the process control system (PCS) based on pressure readings from inside the pig trap to open the closure door.
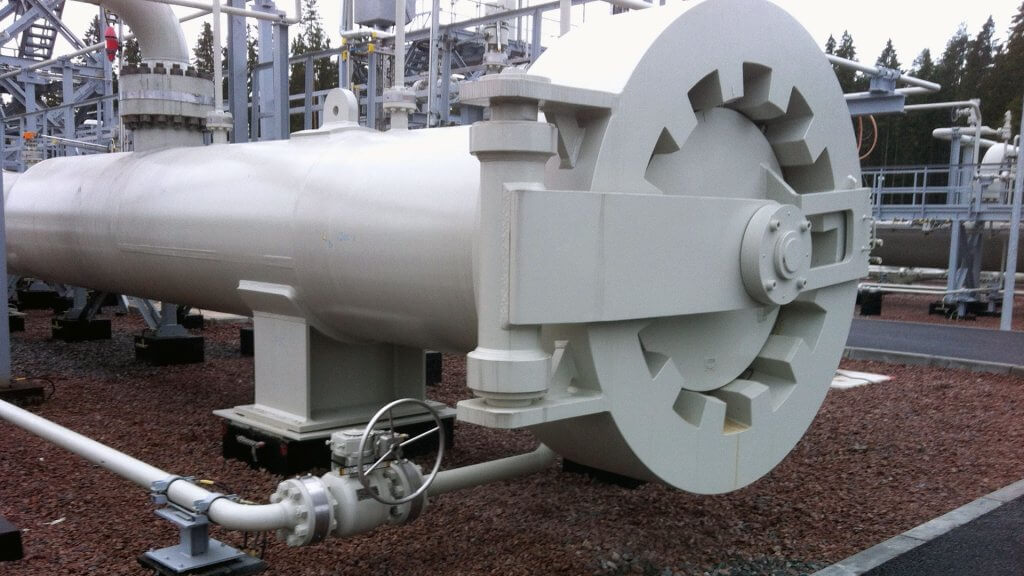
Need for improved safety solutions
Increasing complexity in functional requirements from pig traps, like mobile pig traps, combination launchers-receivers, high-frequency pigging, and pigging on long-distance pipelines, call for an improved and highly functional safety solution connected to the PCS.
Advantages of an Industry 4.0 solution
Solutions connected to the PCS offer a host of benefits including real time visibility across multiple facilities, administrative control, efficiency, and flexibility in operation. The solution is designed to prevent errors and the operator is guided through the procedure.
Local Pigging Control Panel
A Local Pigging Control Panel (LPCP) is a pigging process controller, which replaces both the MPCU and the EPCU. It is equipped with uniquely coded electronic key positions for captive keys, equipped with a limit switch to detect the presence of the key and a solenoid to trap the key till a permissive is received. The LPCP is equipped with a PLC, or an industrial computer, which is programmed to control the sequence of operation and manages the permissive to release the captive keys from the respective electronic key positions.
Real-time availability of process parameters
The LPCP is in bi-directional communication with the PCS. All process parameters like pipeline pressure, pig trap pressure, temperature, pig location, the open and close status of each valve, progress through the pigging sequence, and many others, are available in real-time, offering visibility locally through the LPCP and remotely to all stakeholders through the PCS and the network. Any errors or anomalies are highlighted immediately and can be displayed on the SCADA system in the control room.
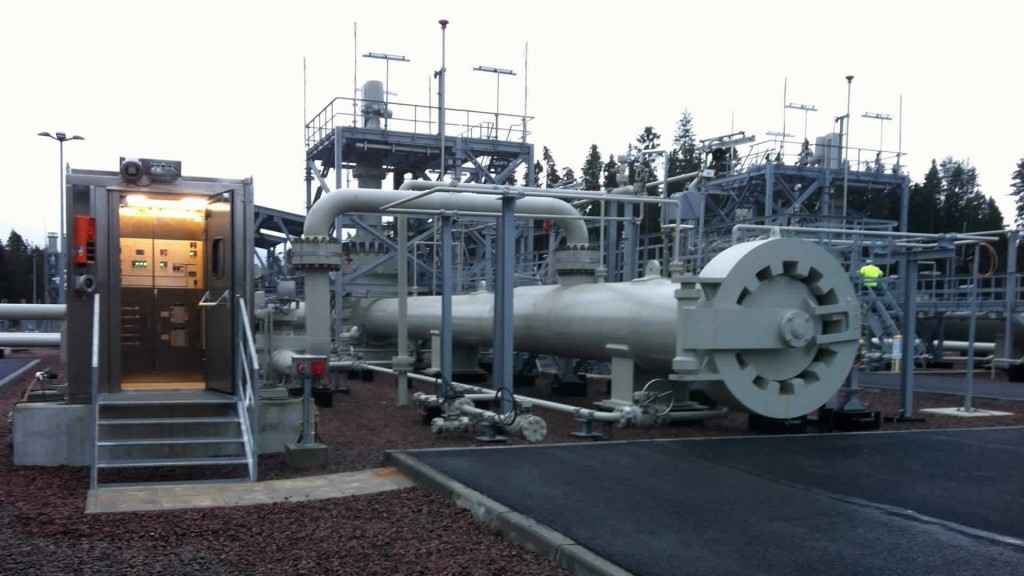
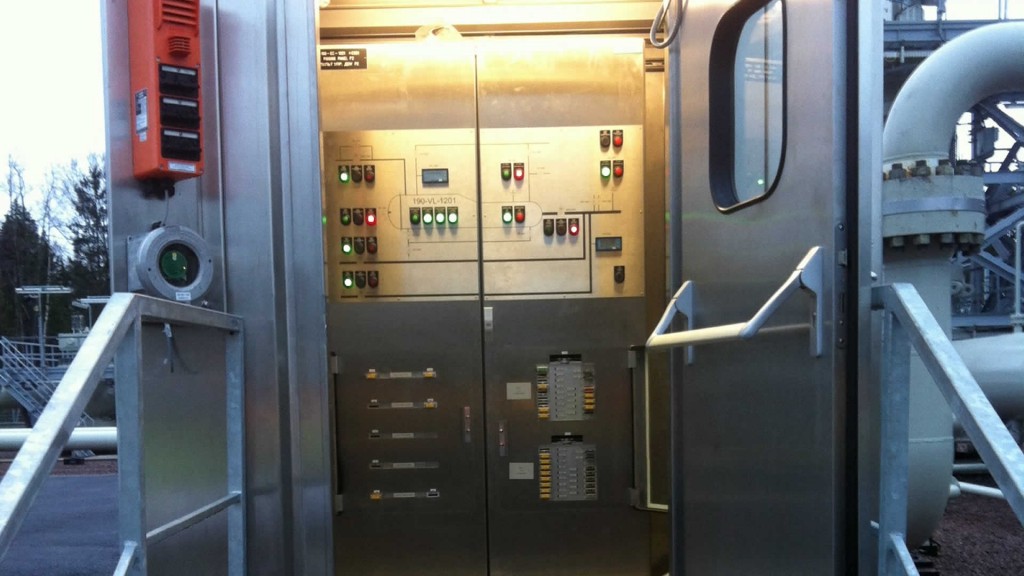
Integration with other process equipment
Motor operated valves equipped on valves, for example, bypass valves, or kicker valves, can be operated from the LPCP. Other sensors such as pressure transmitters, temperature transmitters, level transmitters, pig signalers, etc. can be integrated directly into the LPCP, or via the PCS, to meet functional process requirements.
Building on existing infrastructure
A digital captive key solution builds upon the existing captive key infrastructure and meets all the requirements, while being cost-effective and can be implemented at scale across facilities. The mechanical interlocks on the valves maintain the independent layer of safety.
Control and track the use of master keys
Master keys are often used by operators to bypass written procedures enforced by mechanical interlocks. These carry safety risks for the process and the operator. The use of master keys from the LPCP will require authorization from the control room. Unauthorized use of master keys can be tracked, and an alert can be displayed on the SCADA system in the control room.
Support for multiple operation modes
Typically, a pig trap is designed to be either a launcher or a receiver and designed for one pipeline. Combined launcher-receivers, or mobile pig traps are employed to reduce the CAPEX and may require multiple operating sequences to safely conduct pipeline pigging. Operators may rely on written procedures to execute such procedures, and this carries high risk. An LPCP can be programmed to support multiple sequences or ‘modes’, where the LPCP will guide the operator through the correct sequence of operation while trapping the keys which lead to wrong operations.
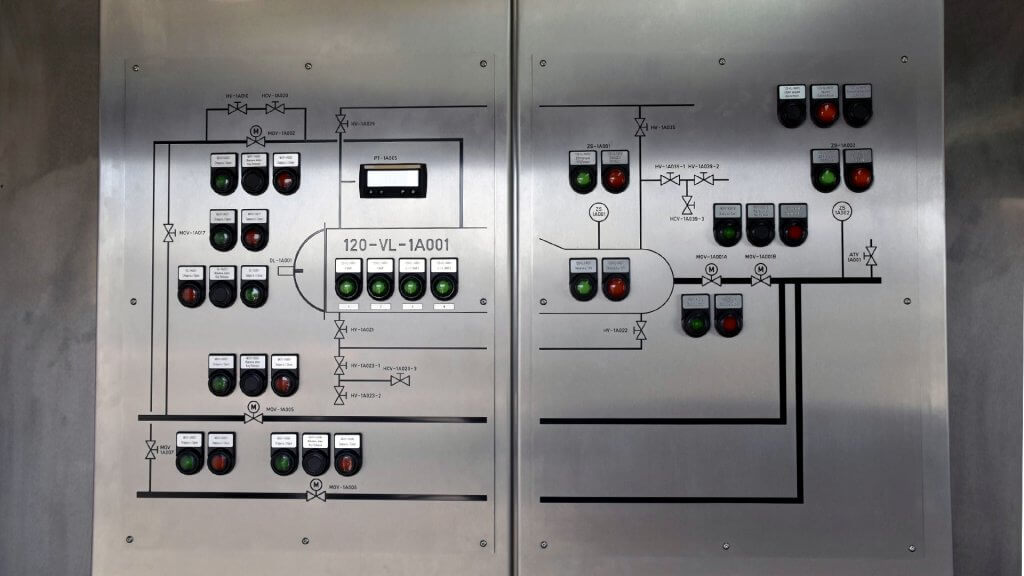
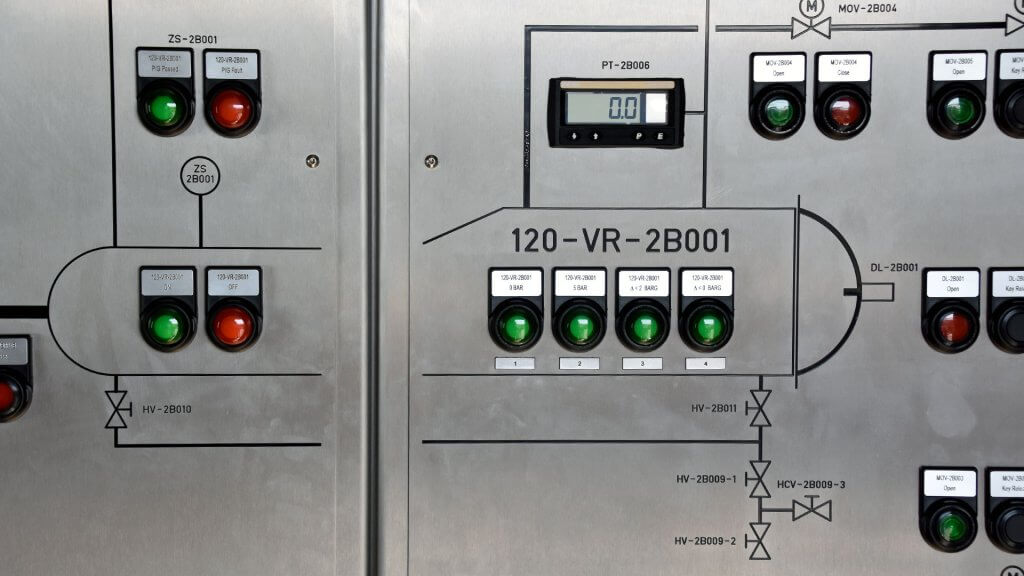
Designed to meet site requirements
The LPCP is designed for use in explosive environments. All the internals are placed inside an ATEX-certified cabinet. Key positions are designed with intrinsically safe components, and all safety-critical components are redundant. Any failures will trigger an alert. Reliable bidirectional communication with the PCS and SCADA is via a glass fiber cable equipped with redundancy. The digital captive key pigging solution and by extension the LPCP is uniquely designed in consultation with the customer to meet functional and safety requirements.